PET Line Self-Man Project
Project Objective
To replace two smaller PET lines with a new single high-speed PET line capable of blow-molding and filling small and large PET formats.
Project Overview
In addition to conveyor systems layout and supply, Descon provided installation supervision services and the complete integration of a high-speed multi- format PET line which included a KHS Blomax-Innofill DRV blow-fill machine, Pressco cap, fill and label inspection, Domino laser coders, Descon W834 Bottle Warmer, (2) Descon Bottle Dryers, (2) Krones labelers, Sentry shell denester, Descon HDTRS Dry Trash Removal Unit, Descon HPS60-04H Shell Washer and Dryer, Standard Knapp SK985 Shell packer, Douglas SPS80 tray-film packer, Douglas M80 film-only packer, Ryson case spirals, Intralox ARB case switch, KHS Innoline palletizer
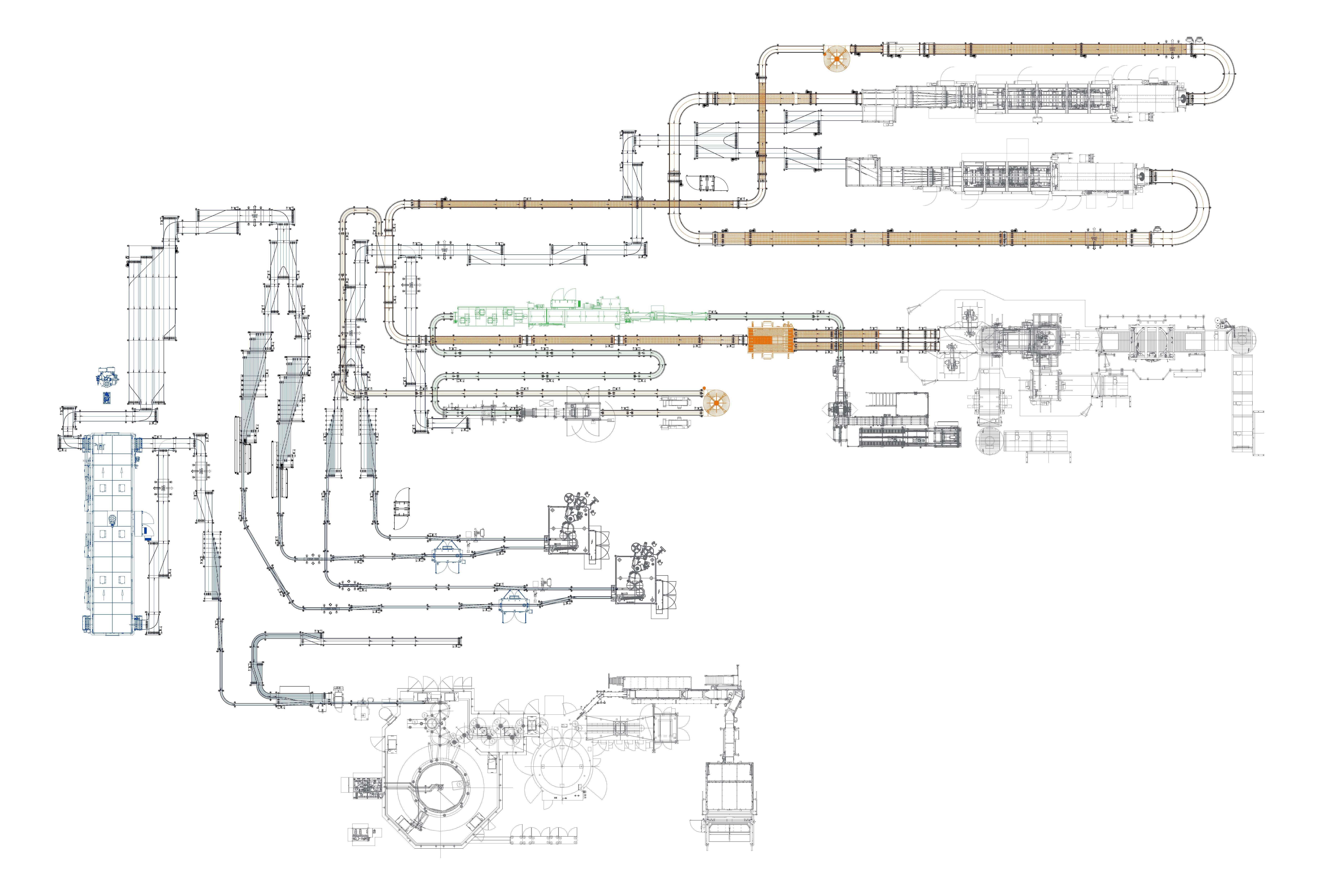
Container Formats / Rates
- 500ml PET @ 900 bpm
- 710ml PET @ 817 bpm
- 1L PET @ 717 bpm
- 2L PET @ 450 bpm
Primary Package Formats
- 8pk shells
- 6pk film-only
- 12pk, 24pk pad w/ film overwrap
Secondary Package Formats
- 4x6pk film-only in tray w/o overwrap
Descon Supply and Responsibility
- Plant layout development
- PET Bottle Warmer
- Model W834 bottle warmer with instantaneous direct-fired gas heating system, chemical injection dosing system, interior marine lighting, upstream and downstream freshwater bottle rinse system
- Full PET delivery system
- Mass conveyance, inline FIFO mass accumulation and dual pressureless single-filing, machine infeed laning and metering system, auto dry lube and internal conveyor cleaning system
- Full PET drying system
- Fully contained drying system with quick-adjust, no-tool air knife adjustment and acoustical sound abatement system
- Empty shell dry trash removal, washing and drying system
- High speed integrated shell cleaning system capable of rates up to 70 shells per minute and including complete with automatic rotating drum filtration system, direct-fired gas heating, integrated exhaust, acoustical enclosure (less than 85 dBA)
- Empty shell conveyance system
- Full pack and case delivery system
- Modular belt conveyors with nose-over type transfers, automatic case guides with DC motor driven changeover (no pneumatics), and Intralox ARB case switch
- Integrated control system
- NEMA 4X motor control panels
- Danfoss OneGearDrive and FCD Distributed Motor control
- EtherNet IP networking between all machine centers
- “Soft” container handling PLC control code
- Operator machine interfaces (HMIs)
- Integrated electrical wireway and plug-and-play cable system
- Installation supervision services
- Start-up and commissioning services